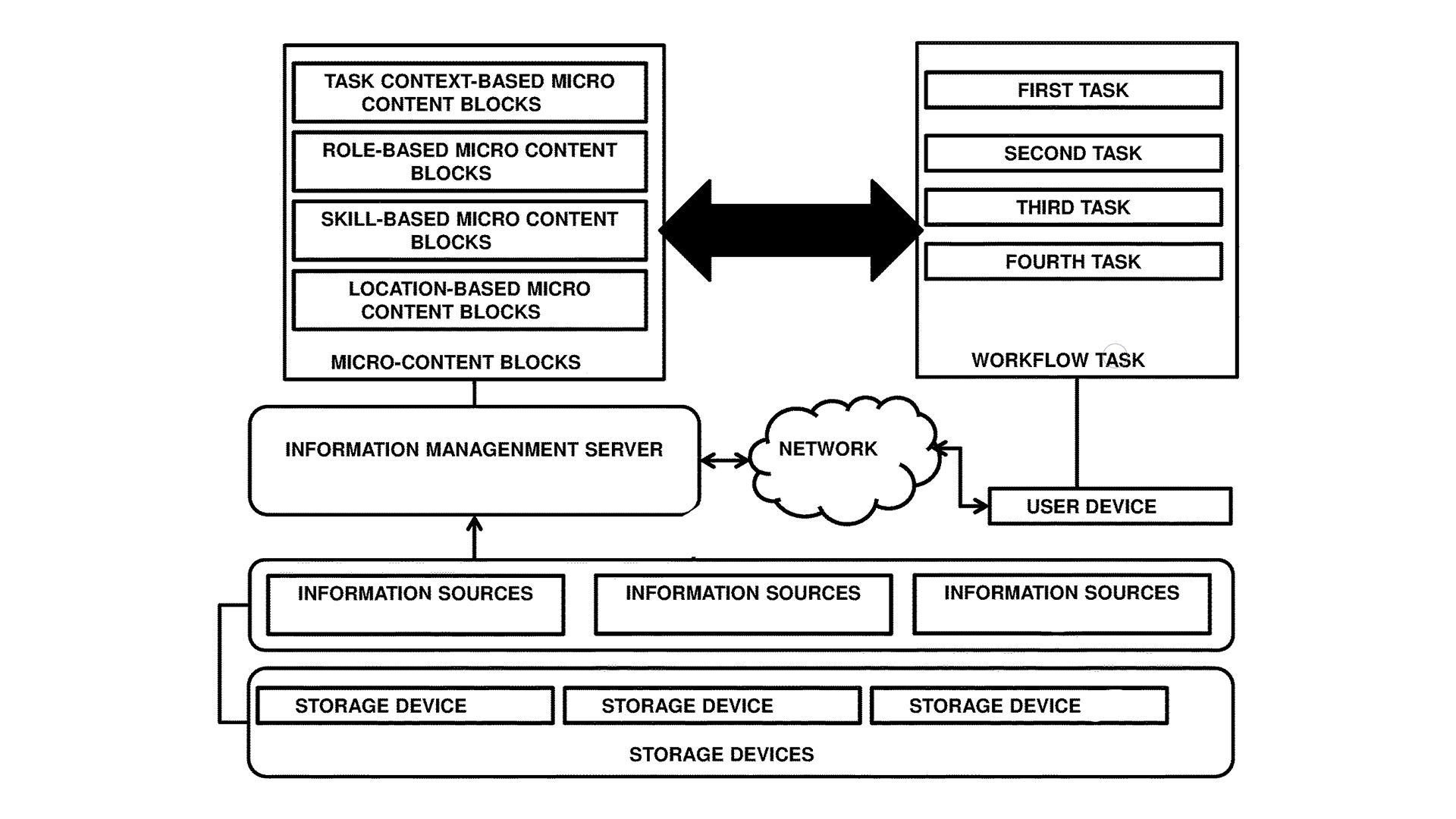
Optimization of operations for digital metrics within networks has become crucial. Automated devices often rely on static, predefined programmable instructions for their operations. While these instructions adeptly handle specific performance metrics, they frequently fail to account for the dynamic and real-time contexts within which these devices operate. This misalignment often leads to a notable divergence between expected and achieved outcomes.
Inherent Limitations of Traditional Systems
Automated devices perform tasks based on fixed instructions that singularly aim to maintain predefined performance metrics. These directives even though are effective under specific conditions, often prove inadequate in diverse real-world scenarios. This modus operandi doesn’t prioritize the desired outcome but sticks to a rigid set of instructions, which may not necessarily align with the evolving requirements of the network or its users.
In numerous situations, deviations between actual performance metrics and their predefined values compel manual intervention or a shift to alternative operational methods. Such manual recalibrations introduce inefficiencies, inconsistencies, and potential errors into the system.
Evolving Toward Real-time Responsive Technologies
To counter the challenges mentioned, a fresh approach to device operation is essential. The new patented technology unveils a groundbreaking electronic evaluation methodology that capitalizes on real-time feedback from validation entities. This approach determines the validity of a fault in a computer-controlled metric appliance. Should the fault be invalid, the technology swiftly modifies the associated predefined programmable instructions.
This responsive mechanism ensures that computer-controlled metric appliances in the network consistently match their expected outcomes, adjusting their operations based on instantaneous feedback.
Incorporating Machine Learning for Enhanced Performance
The methodology detailed in this technology harnesses the capabilities of machine learning and artificial intelligence models. Through a comprehensive analysis of multiple parameters and computer-executable goals, these models suggest a task list that an appliance should pursue to realize its intended outcome.
Integrating machine learning allows the technology to transcend static predefined instructions, providing a dynamic, context-sensitive operation that continually adjusts in response to the network’s changing conditions and real-time user demands.
The highlighted electronic evaluation methodology represents a monumental stride in optimizing computer-controlled metric appliances within networks. By adapting device instructions in real-time and leveraging the prowess of machine learning, the system ensures both the achievement of performance metrics and the broader, overarching objectives of the network.
Functional Capabilities of the Advanced Electronic Evaluation Methodology
Real-time Feedback Analysis and Fault Detection
The advanced technology excels in real-time fault detection for computer-controlled metric appliances. Upon identifying a potential fault based on predefined programmable instructions, the technology liaises with a validation entity. This entity promptly provides feedback on the fault’s authenticity, enabling swift differentiation between actual errors and false alarms, thus augmenting system efficiency and dependability.
Dynamic Instruction Modification
Upon deeming a perceived fault as invalid via real-time feedback, the technology immediately revises the existing programmable instructions. This adaptability ensures the computer-controlled metric appliance functions in tandem with changing scenarios and needs. This recalibration inherently repositions the expected outcome of the computer-executable metric towards optimized performance.
Machine Learning Integration for Task Determination
A standout feature is the integration of machine learning models that act upon numerous parameters and a defined computer-executable goal. This integration facilitates the formulation of an apt computer-executable task list, custom-made for the specific appliance. Consequently, the appliance benefits from a fluid task list, fine-tuned to its environment and engineered to fulfill the delineated goal efficiently.
Outcome Modification and Enhanced Performance
After feedback evaluation, should the fault be genuine, the technology can generate an output signal. This signal proactively instigates a modification in the operation of the affected computer-controlled metric appliance. This alteration indicates the execution of one or more tasks, informed by the updated instruction set. This agile feature ensures the appliance revises and adapts its operations fluidly, assuring peak performance in real-time.
This patented technology amalgamates real-time feedback analysis, agile instruction modification, and the prowess of machine learning. These functionalities merge to provide an unmatched adaptability and efficiency level, ensuring that computer-controlled metric appliances consistently render optimal performance, irrespective of fluctuating and evolving environments.